Personal Commitment
As individuals, the founders of eFuel Pacific have each become increasingly concerned about climate change and the ongoing effects it will have on everyone. This concern is exacerbated by the apparent inability of communities and nations to tackle the problems and make meaningful progress in reducing the impact of the changing climate.
One key issue is the continued increase in use of fossil fuel to support our current energy intensive communities as there is a universal unwillingness to give up on many of the benefits that accrue from this energy use. The solution then is to look to see whether it is possible to replace fossil fuel with energy from renewable sources.
While much good work is being done to shift to direct use of electricity as an energy source, there will be an ongoing need for liquid fuel as the primary energy source for many activities. There is nothing wrong with liquid fuels as they have the significant benefits of being high in energy density (large amounts of energy per unit of fuel), as well as being easy to handle and use.
Society has invested considerable amounts over the years in building infrastructure to store, transport and dispense liquid fuels. Therefore there are huge savings in being able to continue to use this infrastructure. Fuel suppliers also have a great depth of knowledge in how to manage liquid hydrocarbon fuel safely and efficiently, which makes its continued widespread use attractive.
There is a significant unmet demand worldwide for the materials and capacity to produce a new generation of vehicles and devices that can use electricity directly as an energy source. This means that there will be a considerable delay in replacing vehicles and equipment currently burning fossil fuel. Unless they can be supplied with an alternative carbon neutral fuel, they will continue to contribute to climate change.
Synthetic fuel is an obvious answer to this problem, as it is a direct replacement for the equivalent fossil fuel. Using synthetic fuel means that no changes are required to the fuel storage, transport and distribution infrastructure, nor to the vehicles and equipment that uses the fuel. While synthetic fuel may initially be more expensive than fossil fuel, it is certain that the cost of synthetic fuel will reduce over time as efficiencies are discovered and incorporated into the manufacturing plants. It is also certain that the cost of fossil fuels will increase over time as societies start insisting that they meet the true cost of the carbon being released into the atmosphere.
Responding to Climate Change
Climate change is being driven for the most part by human activities with the worst culprit being the addition of greenhouse gasses into the atmosphere. Greenhouse gases trap energy in the atmosphere which causes serious changes to normal climate and weather events.
The most serious greenhouse gas is carbon dioxide (CO2) because it lasts for a long time in the atmosphere. Other greenhouse gases such as methane and nitrous oxide react with oxygen in the atmosphere so their effect is for a much shorter time. Responding to climate change generally means trying to deal with CO2 emissions.
Much work is under way towards reducing emissions, by replacing the use of fossil fuel with clean energy sources such as electric vehicles or decommissioning coal-fired power plants in favour of renewable generation. Another approach to dealing with CO2 emissions is to capture it at the time it is created, such as in an exhaust flue, or to capture it directly from the air. The captured carbon dioxide can then be sequestered underground for very long term storage, or possibly used in an industrial process.
One approach to reduce CO2 emission is to use the captured carbon dioxide as a base material for making liquid fuel, by combining the carbon with hydrogen from water, to produce an energy-dense liquid comprised of a range of hydrocarbon compounds. This is known as synthetic fuel, and has the advantage that it is easy to handle transport and combust using existing technology and infrastructure.
Synthetic fuel is not carbon free, but rather carbon neutral as it is recycling carbon already in the atmosphere. Therefore combusting it does not introduce any new emissions that could drive additional climate change. Using synthetic fuel just recycles carbon already in the atmosphere.
What we do
eFuel Pacific is committed to producing synthetic fuels to replace existing liquid fuel such as petrol, derived from fossil petroleum. The synthetic fuel will be manufactured by combining readily available carbon dioxide in the air with hydrogen extracted from water, using only electricity generated from renewable sources.This will result in a clean carbon neutral fuel that does not contribute to climate change when combusted in an engine.
By making synthetic versions of currently available liquid fuels derived from fossil sources, it will be possible to continue to use existing vehicles and equipment without adding to atmospheric carbon dioxide and climate change. This approach allows for a much quicker response to climate change than waiting for existing vehicles and equipment to be upgraded or replaced with alternatives that do not require fossil fuel.
How we do it
eFuel Pacific will work with organisations and partners already involved in the processes used in the manufacture of synthetic fuel. It is not our intention to invent the technology involved, but rather to license it from organisations that have already achieved this. We have identified a number of potential partners globally and are in discussions with them to acquire their technology.
eFuel Pacific plans to establish our first plant in Taranaki. The region is the existing energy hub for New Zealand, and has a number of businesses located there with experience in building and operating plants to exploit energy technologies. Taranaki has ambitious plans for large scale renewable electricity generation in the region to support a synthetic fuel manufacturing plant. There is also a very active regional development agency which provides encouragement and support for new energy businesses to establish in the region..
What is Synthetic Fuel
Synthetic fuel generally refers to a petroleum fuel such as petrol that has been manufactured from raw materials of air and water using electricity. The resulting fuel is liquid energy in the form of the same hydrocarbon chemicals that are found in petrol which has been derived from distillation of fossil petroleum pumped from underground.
The process involves extracting carbon dioxide from the air or perhaps from a more concentrated source such as a flue stack discharging waste from another process. This is purified and combined with hydrogen obtained from the hydrolysis of water via a process known as the Fischer-Tropsch reaction.
The Fischer-Tropsch reaction produces a range of hydrocarbon molecules, from simple gases such as methane up to waxy solids. The conditions applied to the reaction process can be adjusted to give preference to those hydrocarbon compounds that make petrol. The energy stored in the liquid fuel has come from the electricity used to drive the reactions.
Because synthetic fuel is almost chemically identical to the fossil fuel it is replacing, it can be used in place of those fossil fuels without any changes being required to the methods for handling, transporting, or combusting it.
Our Technology
There are several discrete processes involved in making synthetic fuel from carbon dioxide, and water using just electricity. These are:
- Capture the carbon-dioxide from the air (Direct Air Capture or “DAC")
- Splitting water to release hydrogen (Hydrolysis or a similar process)
- Combining the carbon dioxide and hydrogen to produce liquid hydrocarbons (Fischer-Tropsch process)
eFuel Pacific will seek to use the most efficient process for each of these steps that has already been proven in commercial operation elsewhere in the world. We plan to conduct on-going research to continually improve each process in order to reduce the cost and increase the amount of synthetic fuel produced by the plant.
Direct Air Capture
Direct air capture of carbon-dioxide from the atmosphere (also called “DAC”) is the process of passing air through a capture unit and causing the carbon dioxide present at relatively low concentrations to react with a liquid surface or solid matrix to remove it from the stream of air.
The liquid or solid matrix containing the captured carbon dioxide is then subject to a “reversing” process to cause the carbon dioxide to be released where it can be gathered and concentrated and the original liquid or solid matrix can be returned to capture more.
There are a variety of possible processes using different liquid solutions or solid matrices that can be deployed for direct air capture, each of which has its own advantages and disadvantages.
The key point of direct air capture is that because it requires only air and energy (usually electricity) for the process to work, a plant can be built almost anywhere. This makes it attractive to use sites that have no other immediate use, and in particular it does not cause undesirable land use change, in which an existing activity is displaced.
Flow diagram of direct air capture process using sodium hydroxide as the absorbent and including solvent regeneration.
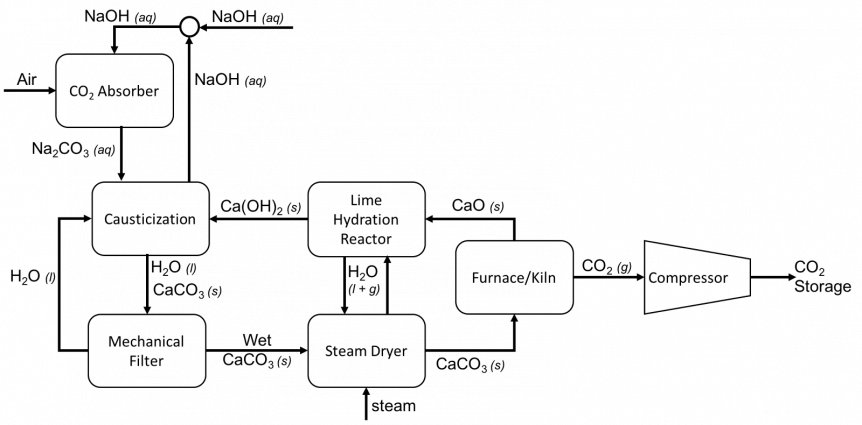
Hydrogen Production
The process of splitting water into hydrogen and oxygen using electricity is called hydrolysis. If the electricity used has been generated from renewable sources, then the hydrogen is called green hydrogen.
There are several alternative processes for hydrolysis involving different designs of cell, using different electrolytes, and operating at different temperatures. Because of the importance of hydrogen to the future energy environment, there is currently significant research work going into improving the efficiency of these processes.
Illustrating inputs and outputs of electrolysis of water, for production of hydrogen and no greenhouse gas
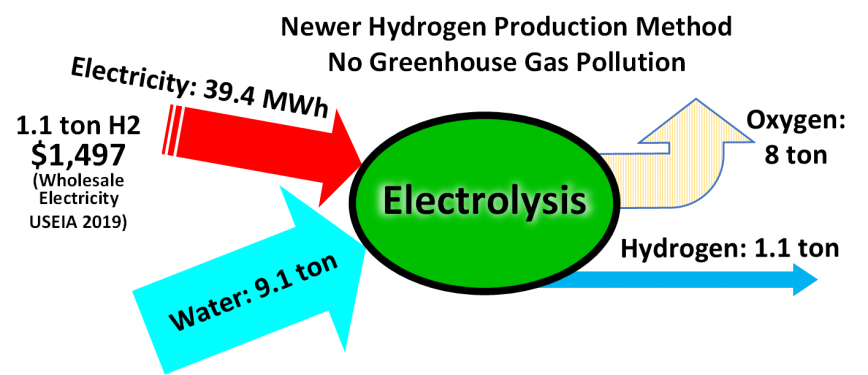
Fischer-Tropsch Process
The Fischer-Tropsch process is a series of chemical reactions that convert a mixture of hydrogen and carbon monoxide (also known as “water gas” or “syngas”) into an array of hydrocarbons in the presence of a metallic catalyst. These reactions occur at temperatures in the range of one hundred to a few hundred degrees, and at pressures of one to a few tens of atmospheres. The process was first discovered by Franz Fischer and Hans Tropsch in Germany in 1925.
The Fischer-Tropsch process has been used to produce synthetic hydrocarbon fuel from coal and natural gas in a wide range of applications since its discovery. In particular it has been used to supplement petroleum based fuels during times of shortage such as during wars or when oil has been restricted or its cost has significantly increased. Nations seeking to reduce their reliance on imported oil have invested in plants operating Fischer-Tropsch processes on an industrial scale.
The design of the reactor vessel and the catalyst used for the process has a significant impact on the range of hydrocarbons produced and the efficiency of the process. For liquid fuel it is important that the reaction produce hydrocarbons that are liquid at normal temperatures, which means from about seven to twenty carbon atoms in the chain. Shorter chain hydrocarbons are gaseous and these need to be vented off and combusted. Longer chains are waxy solids which need to be cracked into shorter chain components. Research into improved reactor vessel design and alternative catalysts is ongoing in an attempt to drive efficiency up from the 25% to 50% achieved historically to the theoretical maximum of about 80%.